Während des Arbeitsprozesses des Papierschneiders kommt es zu Situationen, in denen das Papier ungleichmäßig, durchgeschnitten und schräg geschnitten wird. Wie sollen diese Probleme also gelöst werden? In diesem Artikel werden einige Lösungen für häufig auftretende Probleme und einige Methoden zur Maschinenwartung vorgestellt.
Häufige Probleme und Lösungen für Papierschneider
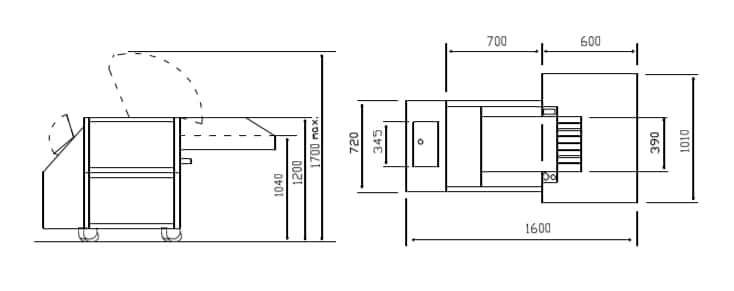
- Messer entladen, schärfen und laden: Wenn die Maschine nicht durchschneiden kann, müssen Sie das Messer schärfen. Gehen Sie zum Schärfen des Messers zu einem professionellen Schärfbetrieb. Befolgen Sie nach dem Schärfen den Vorgang zum Entladen des Messers und installieren Sie dann das Messer. Im Allgemeinen ist das geschärfte Messer schmaler als das Originalmesser. Zu diesem Zeitpunkt sollte das Messer abgesenkt werden. Nimm zuerst eins. Legen Sie das A3-Papier unter das Messer, senken Sie das Messer dann auf den tiefsten Punkt ab, um den Strom auszuschalten, lösen Sie die obere Messerschraube, es gibt drei Einstellschrauben am oberen Teil des Messerhalters, nehmen Sie einen Innensechskant und drücken Sie ihn nach unten, bis Das Papier unter dem Messer ist geschnitten. Es ist alles in Ordnung.
- Schneiden Sie das Papier schräg: Schauen Sie sich zunächst an, welche Seite schräg ist, und schieben Sie dann die Einstellschraube des Breitseitenschiebers nach vorne. Wenn es sich um eine manuelle Maschine handelt, lösen Sie die Schraube unter der Linealstange, stellen Sie die Linealstange ein und befestigen Sie die Schraube.
- Kein Papierdrücken: Überprüfen Sie zunächst, ob Schmutz oder Bücher die Infrarotwand auf der Tischoberfläche blockieren. Wenn ja, entfernen Sie es bitte und prüfen Sie, ob die oberen und unteren Grenzsensoren der Papierpresse falsch ausgerichtet sind. Wenn die Position nicht korrekt ist, justieren Sie den Sensor. Wenn alles normal ist, müssen Sie die Papierpresse überprüfen. Wenn es ein Problem mit dem Motor, dem Platten-Encoder und dem Encoder-Sensor gibt, wenden Sie sich bitte an den Händler, um einen Techniker für den Austausch der Teile zu vereinbaren.
- Die Klinge funktioniert nicht: Überprüfen Sie, ob der Schnittsensor verschoben ist. Wenn die Position falsch ist, justieren Sie den Sensor. Sollte das Messer auslösen, überprüfen Sie bitte die Vierkantbrücke. Wenn die quadratische Brücke kurzgeschlossen ist, ersetzen Sie die quadratische Brücke, andernfalls muss die Hauptplatine oder die Leistungsplatine ausgetauscht werden. Um die Kante des geschnittenen Papiers flach zu machen, muss sichergestellt werden, dass die Schneidkante der Papierschneideklinge scharf ist und der Schärfwinkel angemessen ist. Beim Schneiden von weichem Papier sollte der Schärfwinkel der Klinge 160 betragen; Beim Schneiden von Pappe und Kraftpapier sollte der Schärfwinkel der Klinge 20 betragen. Geeignet; Beim Schneiden häufig verwendeter Druckpapiere sollte der Schärfwinkel der Klinge 210 betragen.
Wartung des Papierschneiders
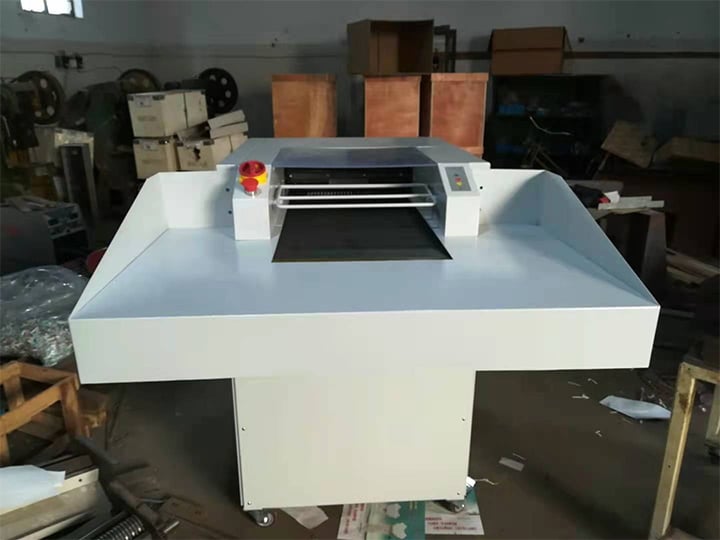
- Reinigen Sie den Motor. Entfernen Sie rechtzeitig Staub und Schlamm außerhalb des Motorsockels. Wenn die Umgebung staubig ist, reinigen Sie sie am besten einmal täglich.
- Überprüfen und reinigen Sie die Motorkabelanschlüsse. Überprüfen Sie, ob die Anschlussschrauben des Anschlusskastens locker oder verbrannt sind.
- Überprüfen Sie die Schrauben jedes festen Teils, einschließlich Ankerschrauben, Endabdeckungsschrauben, Lagerabdeckungsschrauben usw. Ziehen Sie die lose Mutter fest.
- Überprüfen Sie das Getriebe, prüfen Sie, ob die Riemenscheibe oder Kupplung fest sitzt, beschädigt ist und ob die Installation fest ist. ob der Gürtel und seine Kupplungsschnalle intakt sind.
- Wischen Sie beim Starten der Motorausrüstung rechtzeitig den äußeren Staub ab. Wenn Sie genug davon haben, wischen Sie die Kontakte ab und prüfen Sie, ob die Verkabelungsteile Brandflecken aufweisen und ob das Erdungskabel in Ordnung ist.
- Inspektion und Wartung von Lagern. Lager sollten nach einiger Zeit gereinigt und durch Fett oder Öl ersetzt werden. Die Zeit für die Reinigung und den Ölwechsel sollte von den Betriebsbedingungen des Motors, der Arbeitsumgebung, der Sauberkeit und der Art des Schmiermittels abhängen. Es sollte alle 3-6 Arbeitsmonate einmal gereinigt und das Fett erneut gewechselt werden. Wenn die Öltemperatur hoch ist oder der Motor schlechten Umgebungsbedingungen und mehr Staub ausgesetzt ist, reinigen und wechseln Sie das Öl häufig.
- Inspektion der Isolierung. Die Isolierfähigkeit des Isoliermaterials variiert mit dem Trockenheitsgrad, daher ist es sehr wichtig, die Trockenheit der Motorwicklungen zu überprüfen. Das Vorhandensein von Faktoren wie einer feuchten Arbeitsumgebung des Motors und korrosiven Gasen im Arbeitsraum führt zur Zerstörung der elektrischen Isolierung. Am häufigsten kommt es zu einem Erdschluss der Wicklung, d. h. zu einem Isolationsschaden, der dazu führt, dass das stromführende Teil mit Metallteilen kollidiert, die nicht stromführend sein sollten, wie z. B. dem Gehäuse. Ein solcher Fehler beeinträchtigt nicht nur den normalen Betrieb des Motors, sondern gefährdet auch die Sicherheit von Personen. Daher sollte beim Betrieb des Motors der Isolationswiderstand regelmäßig überprüft und darauf geachtet werden, ob die Erdung des Motorgehäuses zuverlässig ist.
- Zusätzlich zur regelmäßigen Wartung des Motors gemäß den oben genannten Punkten ist nach einem Betriebsjahr eine größere Reparatur erforderlich. Der Zweck der Überholung besteht darin, eine gründliche und umfassende Inspektion und Wartung des Motors durchzuführen, fehlende und verschlissene Komponenten des Motors zu ergänzen, Staub und Schmutz innerhalb und außerhalb des Motors vollständig zu entfernen, die Isolierung zu überprüfen, die Lager zu reinigen und zu überprüfen ihre Abnutzung. Finden Sie Probleme und beheben Sie sie rechtzeitig.